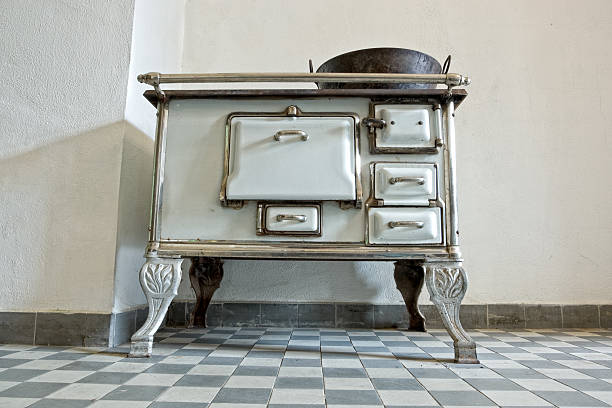
Surface Prep: Before & After Blasting
Updated: December 22, 2023If you run a business in manufacturing or industrial sectors, abrasive blasting is likely a critical part of your daily operations. While the term "sandblasting" is still used, it's important to note that modern processes rarely use actual sand anymore. Instead, the focus is on proper surface preparation, which is essential for ensuring that coatings adhere correctly.
Abrasive blasting plays a key role in preparing surfaces for coatings and finishes. It not only improves adhesion but can also result in a clean, smooth final appearance. Whether you're painting, powder coating, or applying another type of finish, surface prep is the foundation of success.
Ready to take your process to the next level? Contact us today to learn more about our solutions.
The Importance of Proper Surface Preparation
Proper surface prep is crucial because skipping this step can lead to poor adhesion and premature failure of your coating. If paint or any other finish doesn’t stick well, it may peel, chip, or flake off much sooner than expected. This not only looks unprofessional but also increases costs due to rework and maintenance.
Starting with a clean, properly prepared surface ensures better performance, durability, and aesthetics for your components. It’s an investment that pays off in the long run by reducing downtime and improving product quality.
Sandblasting and Surface Preparation
While "sandblasting" was once a common term, it has largely been replaced by "abrasive blasting" due to health and safety concerns related to silica dust. Today, abrasive blasting refers to a broader range of techniques using various media like glass beads, aluminum oxide, silicon carbide, and even natural abrasives such as corn cob or walnut shells.
Each type of abrasive has unique properties, and choosing the right one depends on your specific needs, budget, and desired outcome. Our team can help you select the best media and equipment to achieve the ideal surface finish for your application.
There are also different methods available depending on your setup:
- Air Blast Equipment
- Centrifugal Wheel Blast Equipment
- Blast Cabinets and Portable Units
Let us guide you in selecting the right system to meet your production goals.
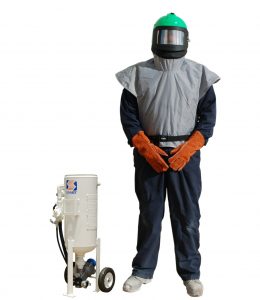
Cleaning After Blasting
After blasting, your surface should be in a clean, raw state ready for the next step. Be sure to apply your finish promptly—especially if working with iron-based materials, which can rust quickly. If there's a delay, consider using rust inhibitors to protect the surface until you're ready to coat it.
It’s also important to keep your blasting media clean and dry. Contaminants or moisture can reduce efficiency and affect the quality of your work.
Connect With Us at Finishing Systems
At Finishing Systems, we offer a full range of equipment and abrasive media tailored for all your blasting needs. Whether you're looking for portable blast units, turnkey blast rooms, or blast cabinets, we have the right tools to improve your workflow and boost productivity.
Don’t let improper surface prep slow down your operations. Let our experts help you find the best solution for your business. Contact us today to request a free quote or learn more about our products.
Contact Us Today
Die casting is a manufacturing process in which molten metal is poured or forced into steel molds. The molds-also known as tools or dies-are created using steel and are specially designed for each project. This allows each component to be created with accuracy and repeatability. We can offer many different die casting solutions because of our wide selection of die casting machines.
Die Casting,Aluminium Die Casting Automotive,Aluminum Alloys For Die Casting,Die-Cast Zinc
NINGBO CITY YINZHOU RUICAN MACHINERY CO.,LTD , https://www.china-sandcasting.com